von Arman Karademir & Mehmet Demir
Abbildung 1: Was, wenn dein Herz widerstandfähiger gegen Brüche wäre? [1]
Warum konventionelle Keramiken nicht immer zufrieden stellen
Keramiken sind nichtmetallische und anorganische Werkstoffe. Zu dieser Werkstoffgruppe gehören beispielsweise Steingut oder Porzellan. Die in der Industrie verwendeten Keramiken werden “technische Keramiken” genannt und wurden für den industriellen Einsatz optimiert. Vorteile sind hohe Hitzebeständigkeiten über 1000°C, hohe mechanische Festigkeit und Korrosionsbeständigkeit. Sie sind jedoch auch spröde und tolerieren keine Formänderungen ohne einen Bruch des Materials, sie sind also weder elastisch noch plastisch verformbar. [2, 3, 4] Ein Werkstoff ist elastisch verformbar, wenn er sich von selbst wieder in die ursprüngliche Form begibt. Grund dafür ist das Nachlassen der Kräfte, die diese Verformung verursacht haben. Als Beispiel kann man sich ein Gummiband vorstellen, das man zieht und wieder loslässt. Bei der plastischen Verformung hingegen kehrt der Werkstoff nicht in seine ursprüngliche Form zurück und verbleibt stattdessen in seiner neuen Form. [5] Hier kann man sich beispielsweise eine Büroklammer vorstellen, die man auseinander biegt. Der entscheidende Nachteil bei plastisch verformbaren Werkstoffen liegt also darin, dass der kleinste Fehler oder Kratzer auf der Oberfläche des Materials der Startpunkt für einen Riss sein kann, der dann in einem Bruch mündet.
Was uns keramische Faserverbundwerkstoffe versprechen
Da man Keramiken aufgrund ihrer vorteilhaften Eigenschaften weiterhin in industriellen Anwendungen einsetzen möchte, liegt es nahe, eine Lösung für das spröde Bruchverhalten der Keramiken zu finden. Hierfür wurde mittels verschiedenster Ansätze versucht, dieses Verhalten zu verbessern. Ein Beispiel ist das sogenannte „Whiskern“, bei dem sehr feine und feste Fasern in die Keramik eingebettet werden. Das Whiskern hat sich jedoch durch eine zu geringe Erhöhung des Risswiderstandes, nicht bewähren können. [6] Einen vielversprechenden Ansatz stellen hingegen keramische Faserverbundwerkstoffe dar. Die Idee dabei ist, ähnlich wie beim Whiskern, Fasern zur Verstärkung in die Keramik einzubetten, allerdings handelt es sich dabei um sogenannte “Langfasern” aus Keramik. Erst der Einsatz dieser keramischen Langfasern hat folgende Eigenschaften hervorgerufen:
- höheren Risswiderstand
- höhere Bruchdehnung
- höhere Thermoschockbeständigkeit
Wie werden aber nun die Keramiken genau verstärkt? Dies geschieht einfach erklärt in drei generellen Schritten. Zunächst werden die keramischen Langfasern in den gewünschten Bauteilformen abgelegt und fixiert. Anschließend wird das eigentliche Keramikmaterial zwischen die Fasern eingebracht. Abschließend wird das Bauteil nur noch mittels Techniken, wie z.B. Schleifen, Bohren, Läppen (Glättung von Oberflächen) oder Fräsen final bearbeitet und optional beschichtet.
Sind diese Schritte absolviert, haben wir einen keramischen Faserverbundwerkstoff hergestellt. Dieser verfügt nun über einen erhöhten Risswiderstand, indem die eingebetteten Fasern eine Art Brücke über einen möglichen Riss bilden. Dies ist in Abbildung 2 bildlich dargestellt.
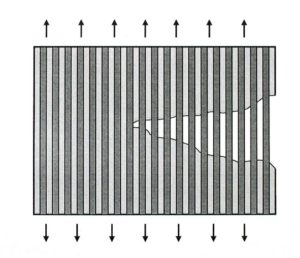
Abbildung 2: Rissüberbrückung an der Rissspitze [7]
Die Risswiderstandskurven aus Abbildung 3 sehen auf dem ersten Blick relativ kompliziert aus – lasst uns diese deshalb kurz erklären. Die SiSiC Kurve (der spitze Verlauf unten links) stellt die Risswiderstandskurve von herkömmlichen Keramiken dar. Zu erkennen ist, dass bei einer bestimmten geringen Belastung, die maximale Dehnbarkeit erreicht wird, d.h. die Risswiderstandskurve sinkt steil. Anders ausgedrückt – das Werkstück aus Keramik bricht. Die restlichen Kurven stellen die Risswiderstandskurven verschiedener keramischer Faserverbundwerkstoffe dar. Bei allen sticht sofort ins Auge, dass diese nicht steil wie die Kurve der herkömmlichen Keramik sinken, sondern eher einen gleitenden Verlauf haben. Dies verdeutlicht die Dehnbarkeit/Biegbarkeit der keramischen Faserverbundwerkstoffe. Somit ist hier der entscheidende Vorteil erkennbar: Keramische Faserverbundwerkstoffe lassen sich dehnen! Wenn auch nicht wie Kaugummi, zumindest deutlich mehr als konventionelle Keramiken. [7]
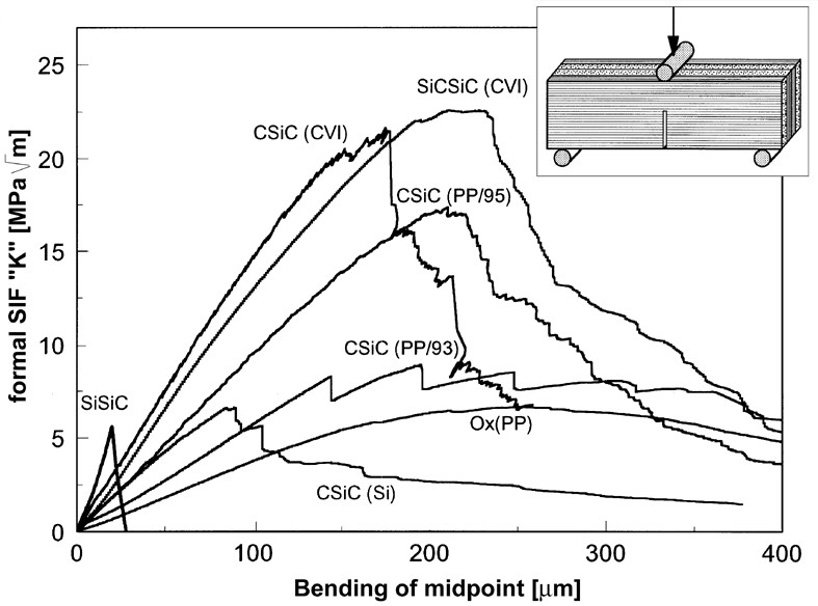
Abbildung 3: Risswiderstandskurven verschiedener kermaischer Faserverbundwerkstoffe und konventioneller Keramik (SiSiC) [3]
Das erwartet uns in Zukunft
Nun sollst du dir hoffentlich unter keramischen Faserverbundwerkstoffen und ihren vorteilhaften Eigenschaften etwas mehr vorstellen können. Vielleicht hast du dir bereits Gedanken zu möglichen Anwendungen gemacht? Auf jeden Fall arbeitet aktuell die Forschung an Entwicklungen für den Einsatz dieser Werkstoffe in einer Vielzahl von Anwendungsgebieten – beispielsweise in der Luft- und Raumfahrt. Sogenannte Raumgleiter, die in der Raumfahrt zum Einsatz kommen, verfügen über Hitzeschutzsysteme und bewegliche Steuerklappen, die beim Wiedereintritt des Raumgleiters in die Erdatmosphäre sehr hohen Temperaturen ausgesetzt werden. Faserverstärkte Keramiken sollen hierbei unter anderem dabei helfen, dass die Komponenten des Raumgleiters temperaturbeständiger werden und die Wiederverwendbarkeit erhöhen. Auch bei Brennern und Heißgasführungen können die keramischen Faserverbundwerkstoffe hilfreich sein. Dabei sind die Brenner und Heißgasführungen vor allem Thermoschocks ausgesetzt, sodass sich der Einsatz der faserverstärkten Keramiken besonders gut eignen würde. Aber auch in der Automobilindustrie, im Rennsport oder in der allgemeinen Fertigungstechnik werden diese Art von Keramiken als vielversprechend eingestuft. Erinneren Sie sich an die Bremsscheiben aus faserverstärkten Keramiken zurück, die höhere Beständigkeiten und längere Lebensdauern vorweisen. Es wird also schnell klar, dass der Einsatz von verbesserten Keramiken viele Potentiale in sich birgt, sodass wir auf Zukünftiges gespannt warten können. [7, 8]
Referenzen
[1] IDEAL Versicherung (2019): Broken-Heart-Syndrom – das gebrochene Herz – Magazin der IDEAL Versicherung. URL: https://www.ideal-versicherung.de/magazin/broken-heart-syndrom-wann-macht-ein-gebrochenes-herz-tatsaechlich-krank/, Abrufdatum: 12.09.2021
[2] Jürgen G. Heinrich (2005): Physikalische und chemische Grundlagen der Keramik. URL: https://video.tu-clausthal.de/videos/inw/vorlesung/tk-ws2009/Physikalische_und_chemische_Grundlagen_der_Keramik%20_Teil_II.pdf#. Abrufdatum: 15.09.2021
[3] Wikipedia (o. J.): Keramik. URL: https://de.wikipedia.org/wiki/Keramik, Abrufdatum: 15.09.2021
[4] Wikipedia: (o. J.): Technische Keramik. URL: https://de.wikipedia.org/wiki/Technische_Keramik, Abrufdatum: 15.09.2021
[5] Lernhelfer (2010): Plastische und elastische Verformung in Physik | Schülerlexikon. URL: https://www.lernhelfer.de/schuelerlexikon/physik/artikel/plastische-und-elastische-verformung#, Abrufdatum: 15.09.2021
[6] Wikipedia (o. J.): Whisker (Kristallographie). URL: https://de.wikipedia.org/wiki/Whisker_(Kristallographie), Abrufdatum: 17.09.2021
[7] Wikipedia (o.J): Keramischer Faserverbundwerkstoff. URL: https://de.wikipedia.org/wiki/Keramischer_Faserverbundwerkstoff, Abrufdatum: 17.09.2021
[8] K. Tushtev, R. Almeida (2018): Oxide/Oxide CMCs – Porous Matrix Composite Systems; Composites With Interface Coatings. University of Bremen, Bremen, Germany.
Das ist ja einmal wieder sehr spannend;)
alles Gute
Nikita