by Maylin Homfeldt, translated by Niko Steiner

Fig.1: On the left is a layered cake, in the middle is a metal component from 3D printing and on the right is Selective Laser Melting (3D printing process). © M. Homfeldt
Pastry chefs use a very similar method to 3D printers – they make their cakes in layers. In doing so, they encounter problems that also arise in metal 3D printing – the layers must be uniform to produce a beautifully shaped cake or a dimensionally accurate component. There are new findings from the science confectionery about how to achieve the uniformity of the layers in metal 3D printing.
The cake
Few desserts can rival a delicious multi-layered cake. A piece of deliciousness that also looks simply delicious. In addition to the outer design, the cutting of a cake is also a highlight. The individual layers inside are revealed. It is important here that the layers remain the same thickness over the entire cross-section of the cake in order to achieve the best visual and taste result and a stable static. Anyone who has tried their hand at making a layered cake will surely agree that it’s not that easy. If the creamy layers that lie between the cake layers cannot be spread evenly because they are not flowable enough, this can lead to problems. Some parts of the cake have no or less filling than others. In my case, I rather unintentionally produced an imitation of the Leaning Tower of Pisa, which got its peculiar appearance from the crookedly cut bases and the irregularly applied layers of cream.
The metal 3D print
Uniform layers are important for cakes as well as for selective laser melting (SLM), which is also called laser-powder-bed-fusion (LPBF). Selective laser melting is an additive manufacturing process (3D printing process in which layers of a material are fused with a high intensity Laser resulting in a solid object) produces metallic components from metal powders. In this process, a thin layer of powder is spread from a powder supply into the print space using a roller. A laser beam then melts the material locally so that the metal powder is bonded at the desired points. The print space is then moved downward by one layer thickness and another layer of powder is applied, so that the component is created layer by layer from fused metal powder (see Figure 1).
During the process, the uniformity and density of the powder layer in the print space is essential, without which height gain and dimensional accuracy in the printed component are impossible. After all layers have been passed through, the component is freed from excess powder and, if necessary, reworked.
The powder must flow
If the metal powders are poorly flowing, in the worst case no powder layer can be built up in the printing chamber and thus no component can be produced (see figure 2). The flowability is determined from the ratio of attractive to weight force. With smaller particles, the attractive force outweighs the weight force, resulting in poor flowability (see figure 3). This can be well illustrated with wet and dry sand. The wet particles in sand stick to each other because the attractive forces between the individual sand particles are very high due to existing liquid bridges. The dry sand has lower attractive forces because there are no liquid bridges and is therefore more flowable.
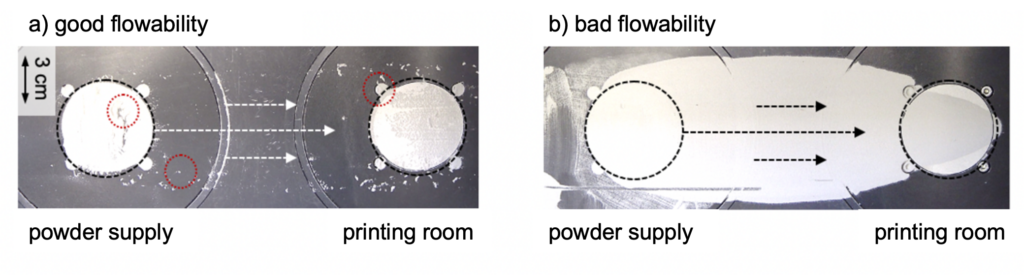
Fig. 2: Illustration of a metal powder with good and poor flowability. A layer of powder is spread from the material supply into the printing chamber. Poor flowing powder is shown on the left and good flowing powder on the right. © E. Gärtner & M. Homfeldt
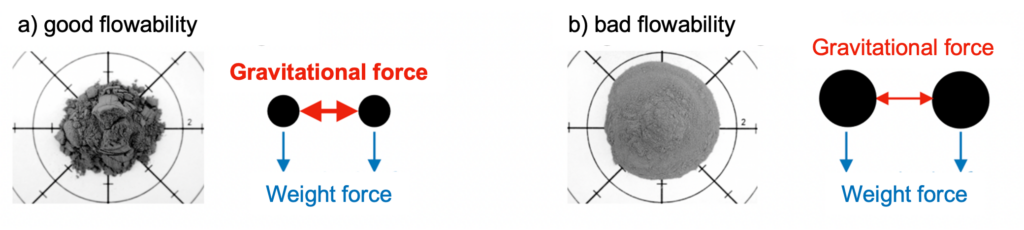
Fig. 3: Photos of good and poor flowing metal powder with diagram of the attractive force and weight force with good and poor flowability. For the smaller particles, the attractive force (thicker arrow) outweighs the weight force, resulting in poor flowability. © E. Gärtner & M. Homfeldt
Production of the metal powder
When the metal powder for 3D printing is produced via gas atomization (disintegration a liquid metal stream into small droplets in a gas) in an inert gas atmosphere (inert gases = gases that are inert to reaction), particles of different sizes are produced. Traditionally, the metal powder produced is elaborately divided into fractions of different particle sizes. This process is called “fractionation”. Fractions of larger particle sizes (particles larger than 20 μm) are used for the 3D production of components. For the fractions with smaller particle sizes, other uses are found in the best case. However, they are ruled out for the 3D printing process because they impair the overall flowablility.
Larger particles are more suitable than the smaller ones because they are more flowable (see Figure 3 and 4). The individual powder layers for the 3D printing process are more easily spread (compare figure 2).
However, it is still possible to use powders with smaller particle sizes for 3D printing and thus significantly increase the amount of metal powder used. For this, however, the attraction force acting between metal particles have to be reduced. The research of Eric Gärtner at the University of Bremen has used a process named nanoparticle dry coating metal powders with smaller particle diameters (<20 μm) applicable to 3D printing (see Figure 4). These are more flowable due to the nanoparticle dry-coating. This is due to the reduction of the attractive forces between the metal powder particles with increasing the interaction distance. With this type of coating, a larger amount of the gas-atomized metal powder can be used, and the process of fractionation can be omitted or simplified.
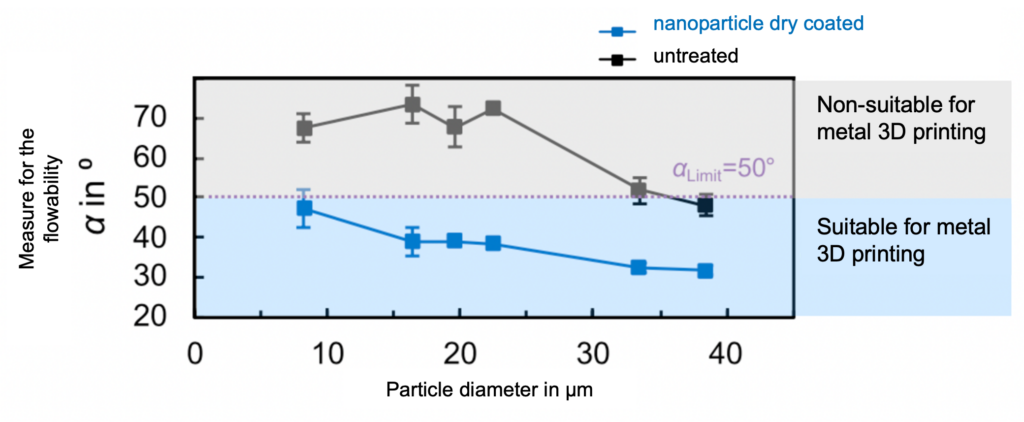
Fig. 4: Measurement of flowability improvement by nanoparticle dry coating of metal powder for different particle diameters. Without nanoparticle dry coating (grey dots), the flowability of the metal powder only decreases strongly enough for the largest particle size tested so that it is suitable for printing. With coating (blue dots), all tested particle sizes are suitable. Modified according to [1].
How the nanoparticle dry coating works
The adhesive (adhering without fusing to the adhesive surface) nanoparticles reduce the forces acting between the particles with creating an artificial surface roughness (see figure 5). The increased surface roughness reduces the attractive forces because the distance between the individual particles is increased. The individual particles therefore no longer hold together as strongly improving the flowability. The flowability improvement phenomenon is due to the size of the nanoparticles and less the material they are made of. The material of the nanoparticles can thus be chosen to match the metal powder used. This freedom from material is crucial for the function of the printed component.
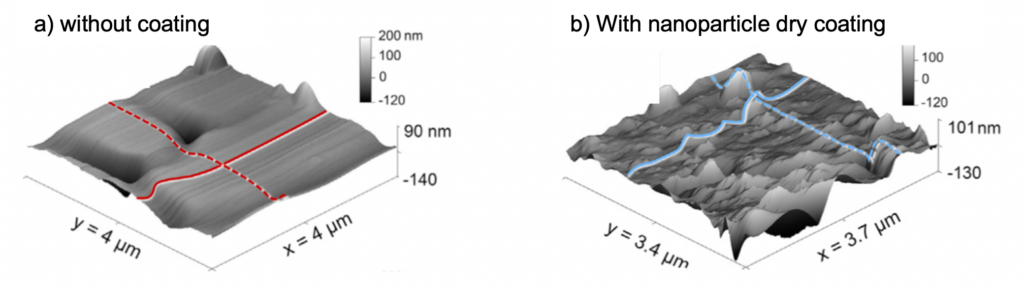
Fig. 5: Figure 5a) shows the surface of an uncoated metal powder particle. Figure 5b), on the other hand, shows the surface of a nanoparticle dry coating. Modified according to [1].
Hungry for more?
You can read more about metal 3D printing at the Leibniz-Institut für Werkstofforientierte Technologien – IWT [2]. A deeper insight into the topic of nanoparticle dry-coating for metal 3-D printing can be found in the paper of Eric Gärtner et al. which is the basis of this article.
Sources
[1] E. Gärtner, H. Y. Jung, N. J. Peter, G. Dehm, E. A. Jägle, V. Uhlenwinkel, and L. Mädler. Reducing cohesion of metal powders for additive manufacturing by nanoparticle dry-coating. Powder Technology, 379:585–595, 2021.
[2] IWT Bremen Website https://www.iwt-bremen.de/de/home
Abb. 1a: https://de.freepik.com/vektoren-kostenlos/geburtstagstorte-eingestellt_3707565.htm#page=1&query=geburtstagstorte&position=4
<a href=’https://de.freepik.com/vektoren/geburtstag’>Geburtstag Vektor erstellt von freepik – de.freepik.com</a>
Abb. 3: modified after [1]
Abb.4: modified after [1]